執筆:EugeneAmnis
なぜなぜ分析
製造現場の品質管理関係の報告書にはほぼ必ずと言っていいほど、なぜなぜ分析と呼ばれるものを入力するための欄が配置されている場合が多いです。今回はこのなぜなぜ分析について記していきます。
原因探求の思考法の一つ
なぜなぜ分析は三段論法と同様、思考法の種類の一つです。発生した問題から5つ遡れば真の原因に辿り着くというシナリオの下で行う連想ゲームとも言えるかもしれません。
例えば、客先に届けたケーキが崩れていたをなぜなぜ分析すると、
- 客先に崩れたケーキを納入
- 運搬中のケーキの固定が甘かった
- 運搬時の梱包のルール(荷姿規定)がなかった
- 荷姿規定の必要性を理解していなかった
- 初めて行う業務形態であった
とこのなぜなぜ分析の結果では経験者を雇うか業務運用に対しての習熟度をチェックする方法を取るかが対策となります。
でも具体的な対策は新しく荷姿規定の策定と周知・教育を徹底することが肝要となるのは明白です。つまり3段階目で真の原因と思われるものに達しているのです。
探求を無理やり進めると人由来の対策になりがちになる傾向があったように思います。
ネットを含めた周囲でも私自身もなぜなぜ分析の使いづらさはよく話題になっていました。品質管理アドバイザーとして現場の指導にあたっていた方もあまり当てにしていない素振りを見せてました。
それでも客先に提出する報告書には入力欄が必ずと言っていいほどあるので若手の頃は無理やり埋めていたものです。ネットの寸評も似たようなものです。ではなぜなぜ分析の意義は何なのでしょうか?
管理部門のためのツール?
多くの現場由来の問題は経済効率性を無視すればすぐに対策ができる場合が多いと感覚的に思っています。現場とは要望を達成するために管理された環境にある領域であることを踏まえれば当然です。
そんな環境で5段階も離れた問題を解決するのは自分の任された領域外で動きなさいと言っているようなものです。その結果、人由来の対策ばかりになってしまうのでしょう。裏を返せば各現場を制御する役割にある管理部門からはなぜなぜ分析を始めた場合は適切な形に収まる場合が多いかもしれません。
因みに例えで出したケーキの問題を管理部門からみると
- 客先に崩れたケーキを納入
- 工場発送時には問題なし
- 運搬中の外観チェックはしていない
- 運搬時のケーキ固定が甘かった
- 運搬時の梱包のルール(荷姿規定)がなかった
とちょっと無理くりな感じもしますが、5段階目の対策を取ることで再発防止になることは明白になります。
言い方を少し変えればなぜなぜ分析は5段階にこだわらなければ、問題解決のための思考法として有効である。また間接的な立ち位置での思考法としても適切であると言えます。
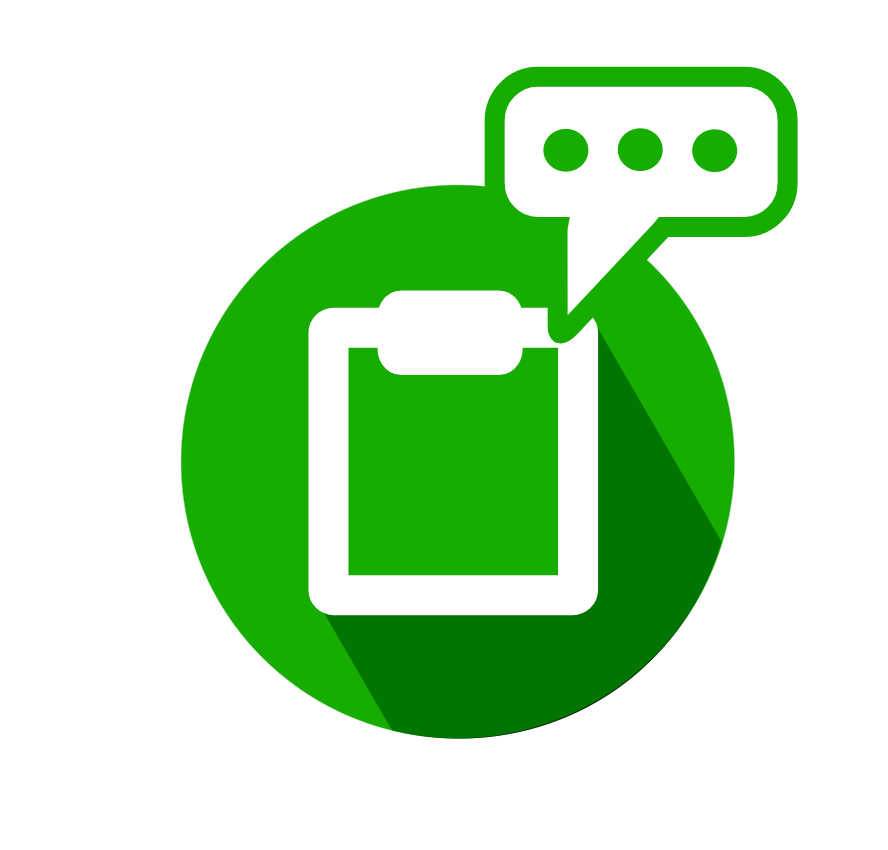
私自身は一般にベテランと呼ばれた頃ぐらいから、客先の報告書であっても5段階に満たない場合は空欄にして提出するメンタルに成長していました。それでも問題にはならなかった所をみると途中からなぜなぜ分析の運用方法自体が疑問視されていたのかもしれません。